SeaDragon
Greetings! Today I'm telling the story about my silver SeaDragon jewelry. It started as a college project, and is still evolving and growing. This sets the stage for the exciting plans I have for next year!
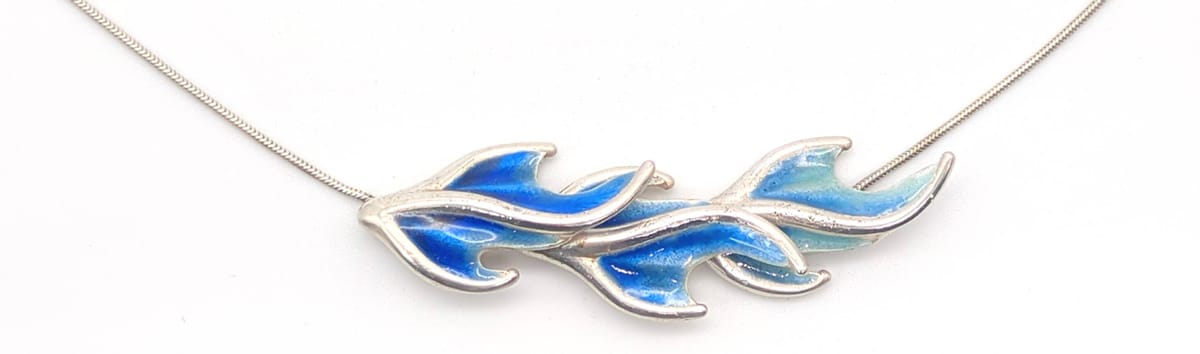
The leafy seadragon (Phycodurus eques) or Glauert's seadragon, is a marine fish. [...] The name is derived from their appearance, with long leaf-like protrusions coming from all over the body. These protrusions are not used for propulsion; they serve only as camouflage.
--Wikipedia page Leafy seadragon
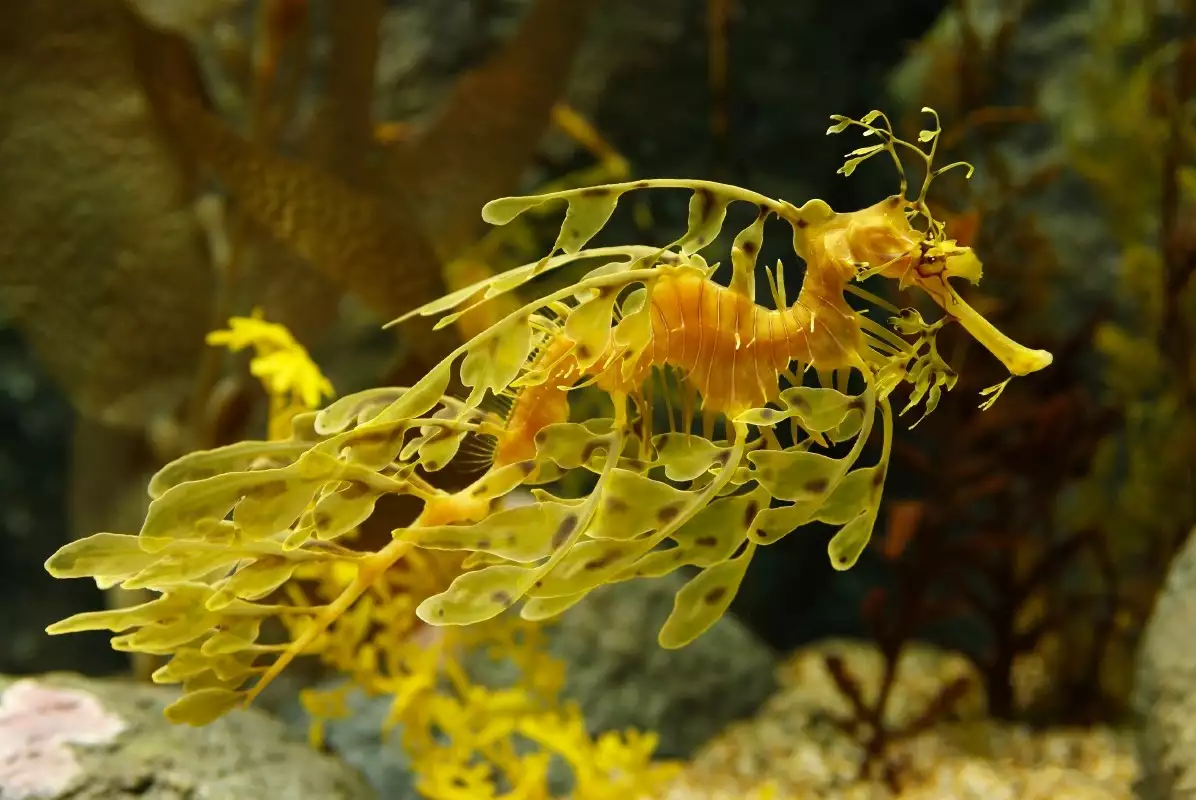
It Looks Like A ___
SeaDragon was inspired by dragons, and by sea horses, and by this not-a-seahorse fish called a leafy seadragon. And also by a vague notion that a lot of art mimics bits of nature like fins and leaves and flowers.
Some people sea manta rays, or dragon scales, or a mermaid's tail. They're all sort of right? Because SeaDragon is a design about flow and movement and little modular pieces that go together.
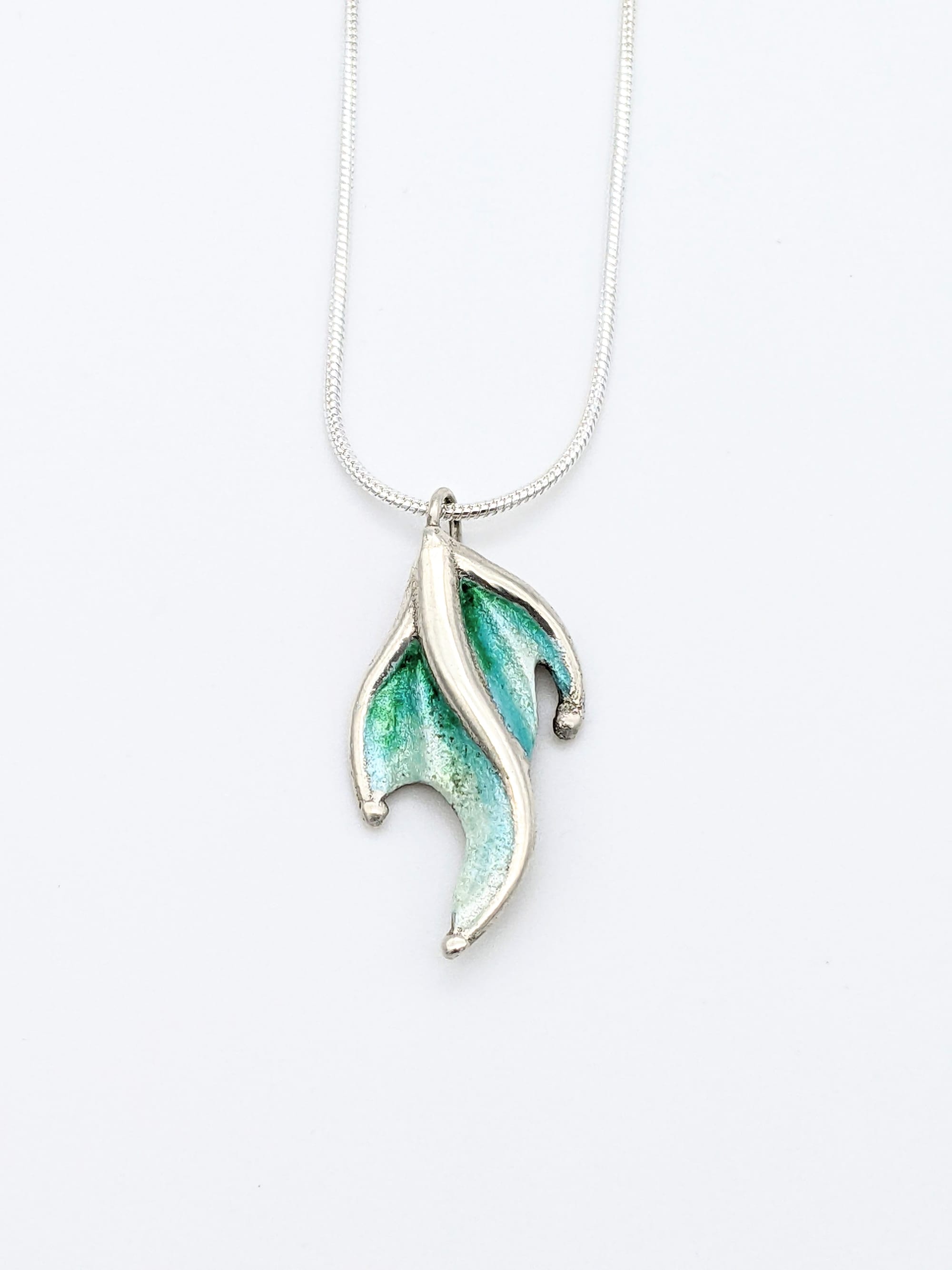
Origin Story
In art college (Savannah College of Art and Design) I took a class on casting. This is where I learned the basics of making vulcanized molds and casting using the lost wax process. By happenstance I also had a 3D modeling class, either the same semester or one previous.
We were assigned a project to design a linkage necklace; a style where each unit of the necklace attached directly to its neighbors, without being threaded like a bead or joined via chain or rings. We could use no more than 3 or 4 pieces - we would need to mold and cast each piece several times, and link them together. This was probably the final project for the casting class.
SeaDragon was that project, originally cast in yellow bronze (cheap) and with flat-back crystals glued on to the points.
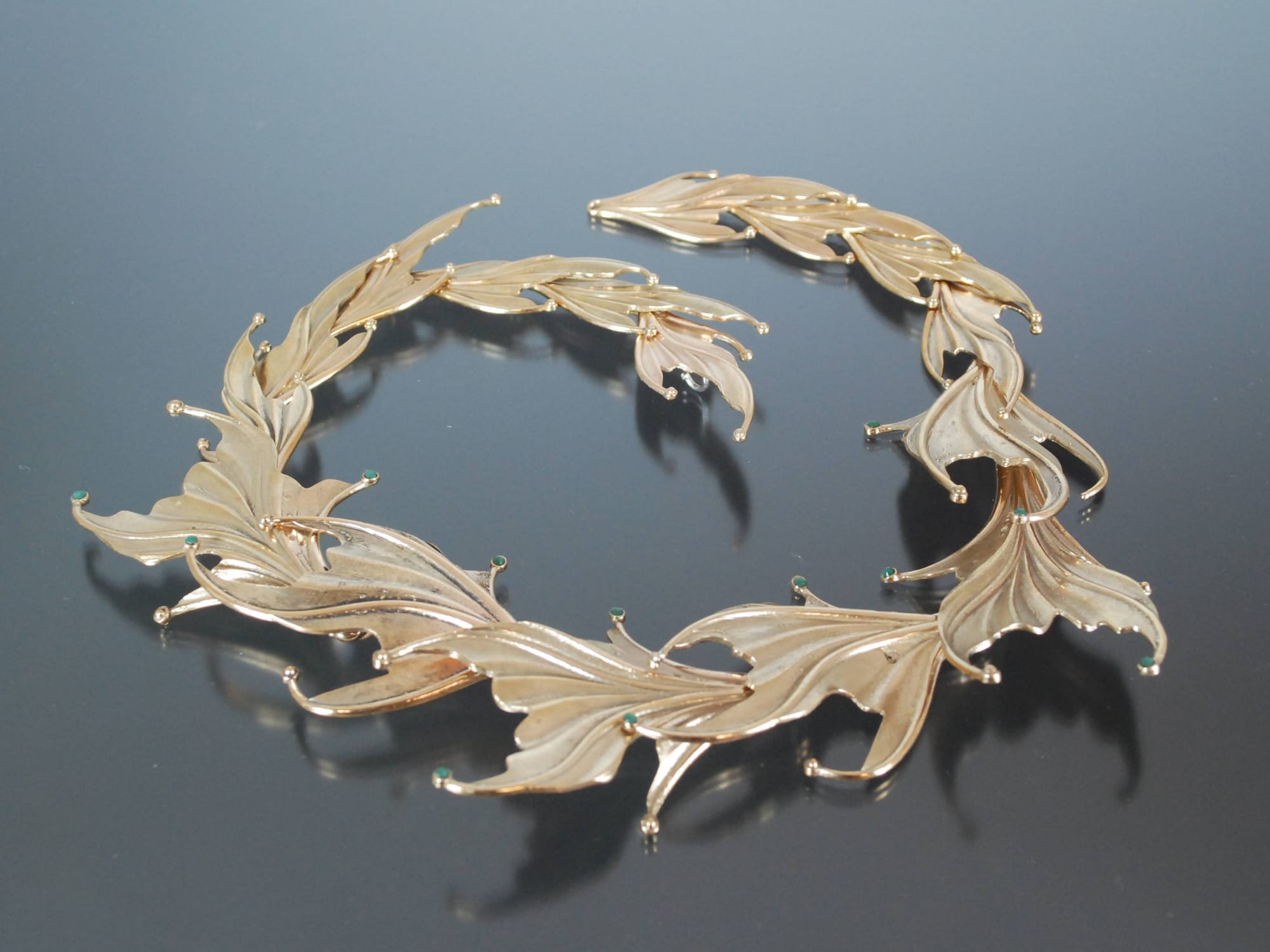
Even though casting class was over, I now had this idea, and these molds, and access to the school's casting lab whenever I wanted. I made another bronze necklace, this one using a mix of different colored bronzes, and wax pieces that hadn't come out of the mold "complete" but still looked very cool.
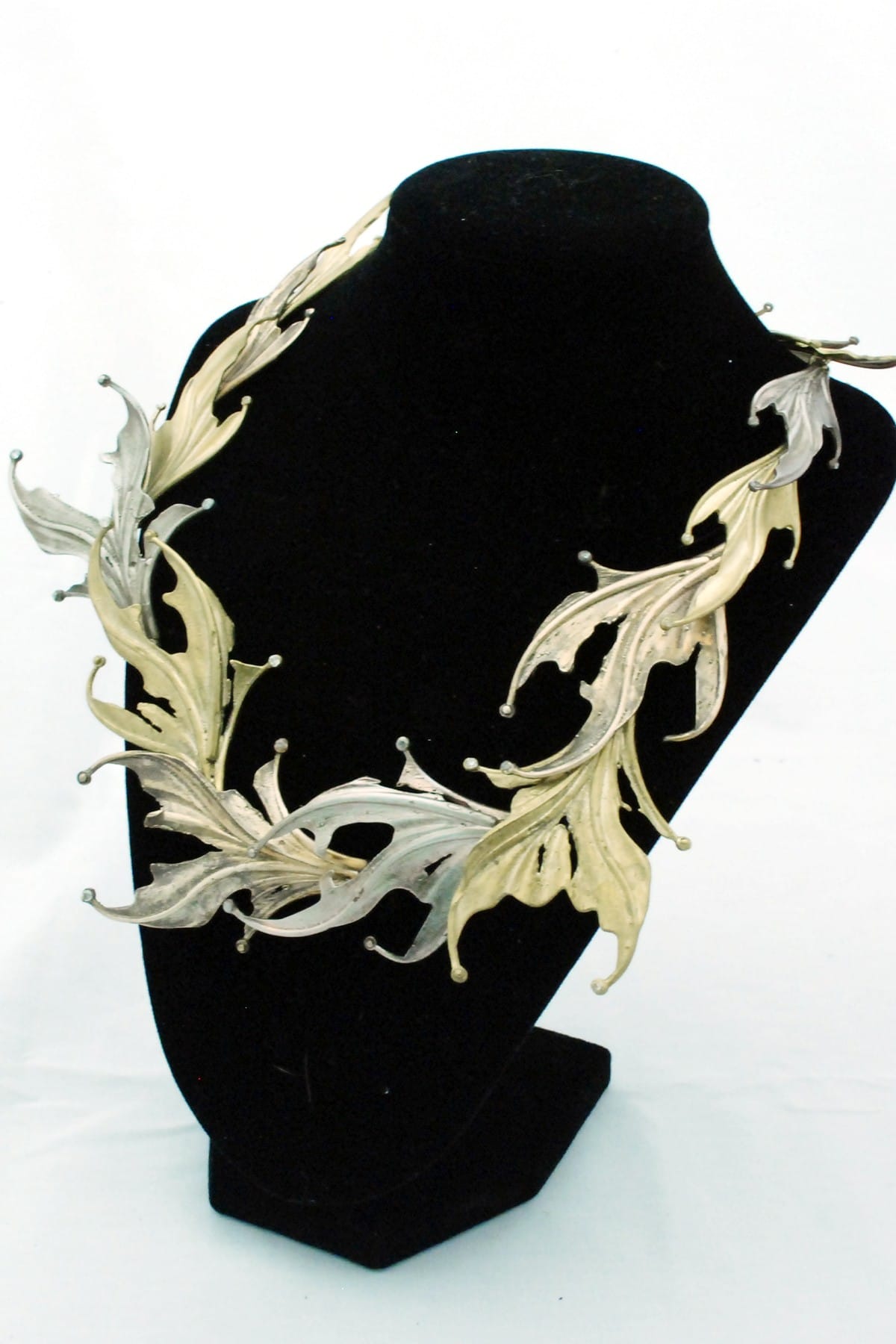
When I had an enameling class, I create a full SeaDragon necklace in fine silver so I could add enamel colors to it. During a class exploring Gold and Platinum, I plated one silver piece in 24K gold, and then had to practice with a laser welder to attach it to another silver piece.
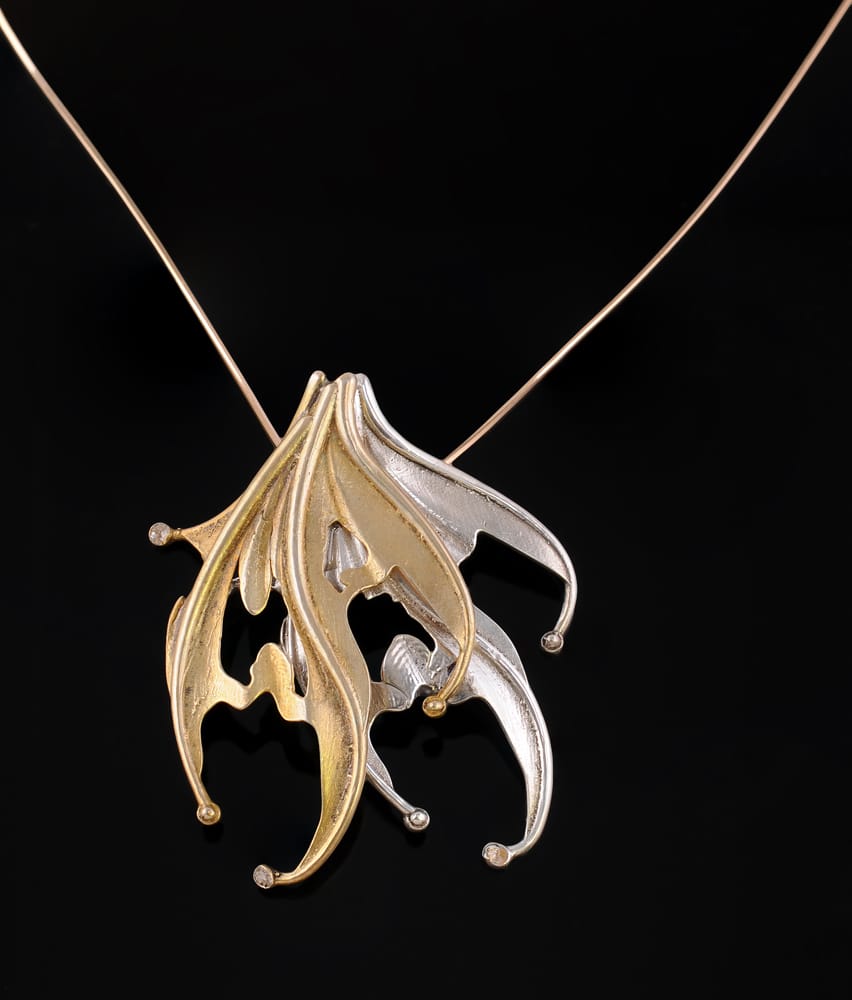
After graduating and moving away, I didn't have access to the tools and equipment anymore, but I had purchased my own copy of the 3D modeling software. SeaDragon II took shape over the next few years; I was trying to design something smaller (and lighter) without losing the free flowing shape and texture.
About The Texture
One of the secret details of SeaDragon that I love dearly is the texture on the fins. It looks almost like the lines on a topographical map.
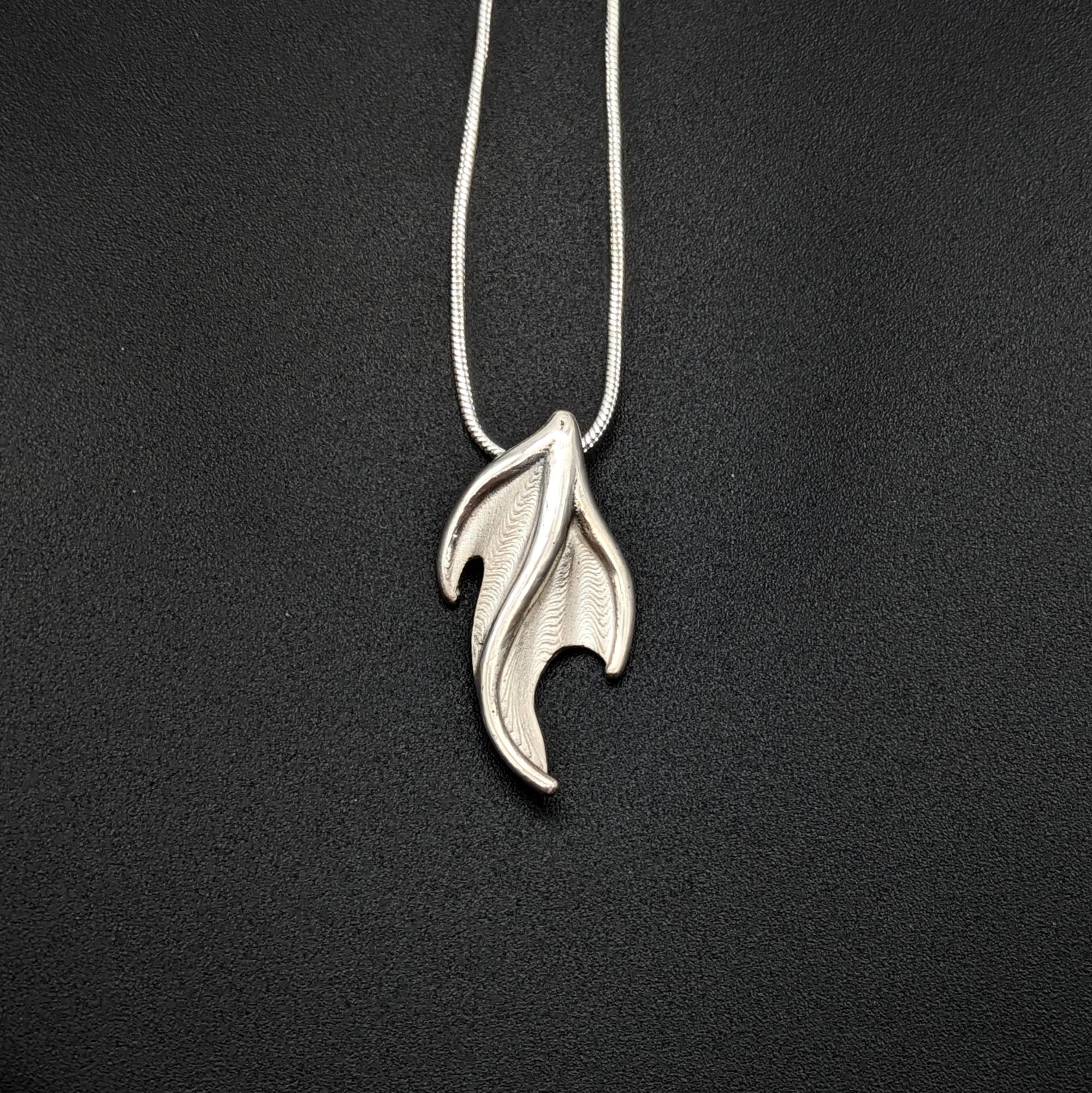
This is purely an accident of the origin. The original models were printed on a wax printer at the school lab - a resource in heavy demand. (And remember that 3D printers of any kind were bigger, slower, and more expensive in 2009.) In order to print faster, the lab used a low resolution to print - basically printing in fewer thick layers instead of many thin layers. The texture on the SeaDragon is from those printing layers. I liked it so much I kept it on the originals, and tried to preserve the texture on SeaDragon II.
About the Color
Enameling on fine jewelry is hard.
I took one class on it in college. Some artists spend most of their lives specializing in enamels in order to perfect it.
Vitreous Enamel is basically glass. I use powdered enamels, which are specialty blends that have all of the ingredients necessary to melt into colorful, durable glass. The enamel powder is applied to a piece of metal, then the whole thing is heated until the ingredients melt and combine. For what I am currently using, that temp is generally above 1400 F.
There are a number of challenges. The enamels I use are applied as a powder - colors don't mix like paint. Most blending is done through layering instead. Meanwhile, some colors (especially reds and pinks) react with copper or silver, and go yellow or opaque.
But if everything goes well, look what you can do with it!
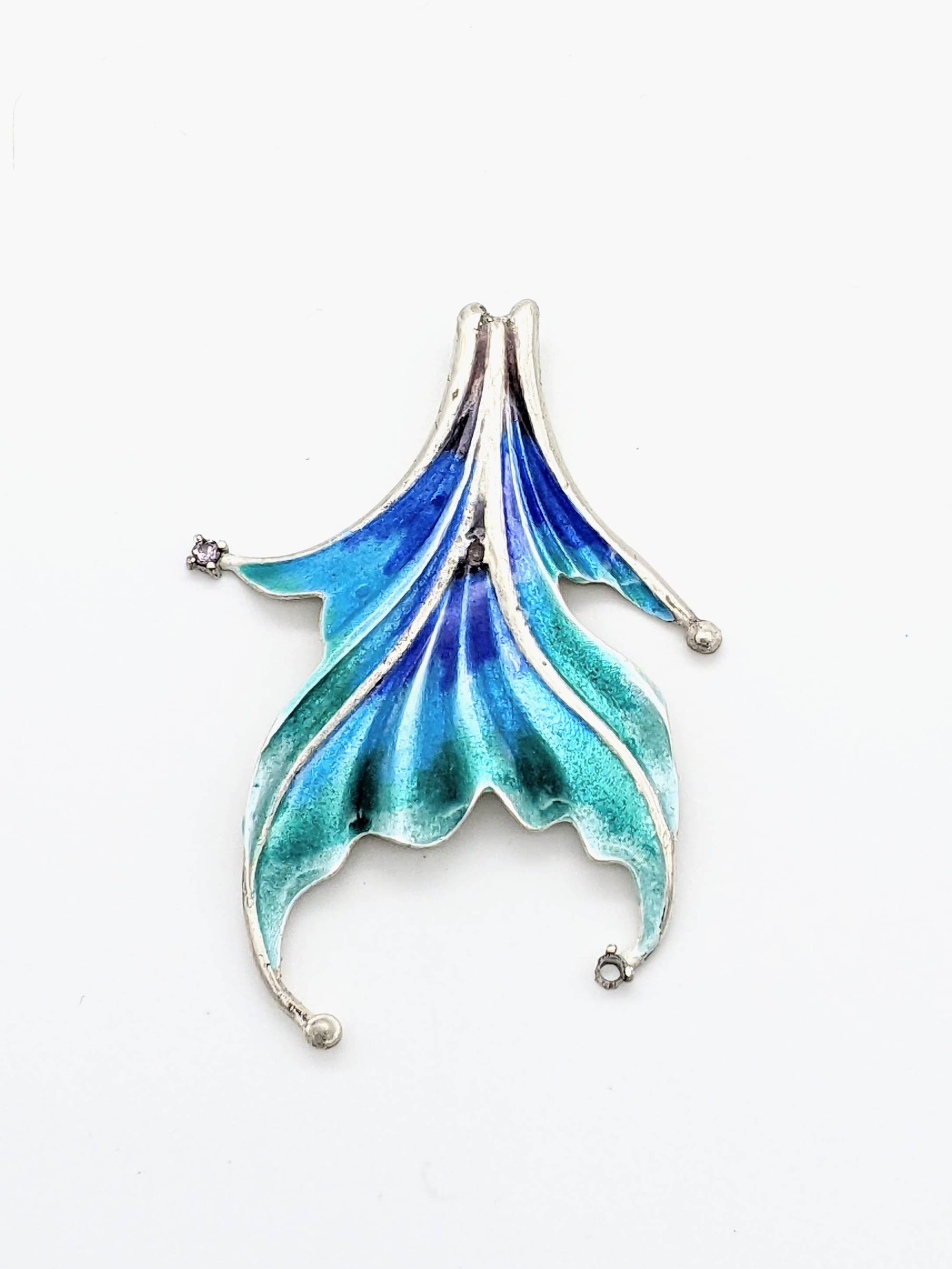
About the Shapes
SeaDragon keeps evolving. It started out chunky. Then got smaller.
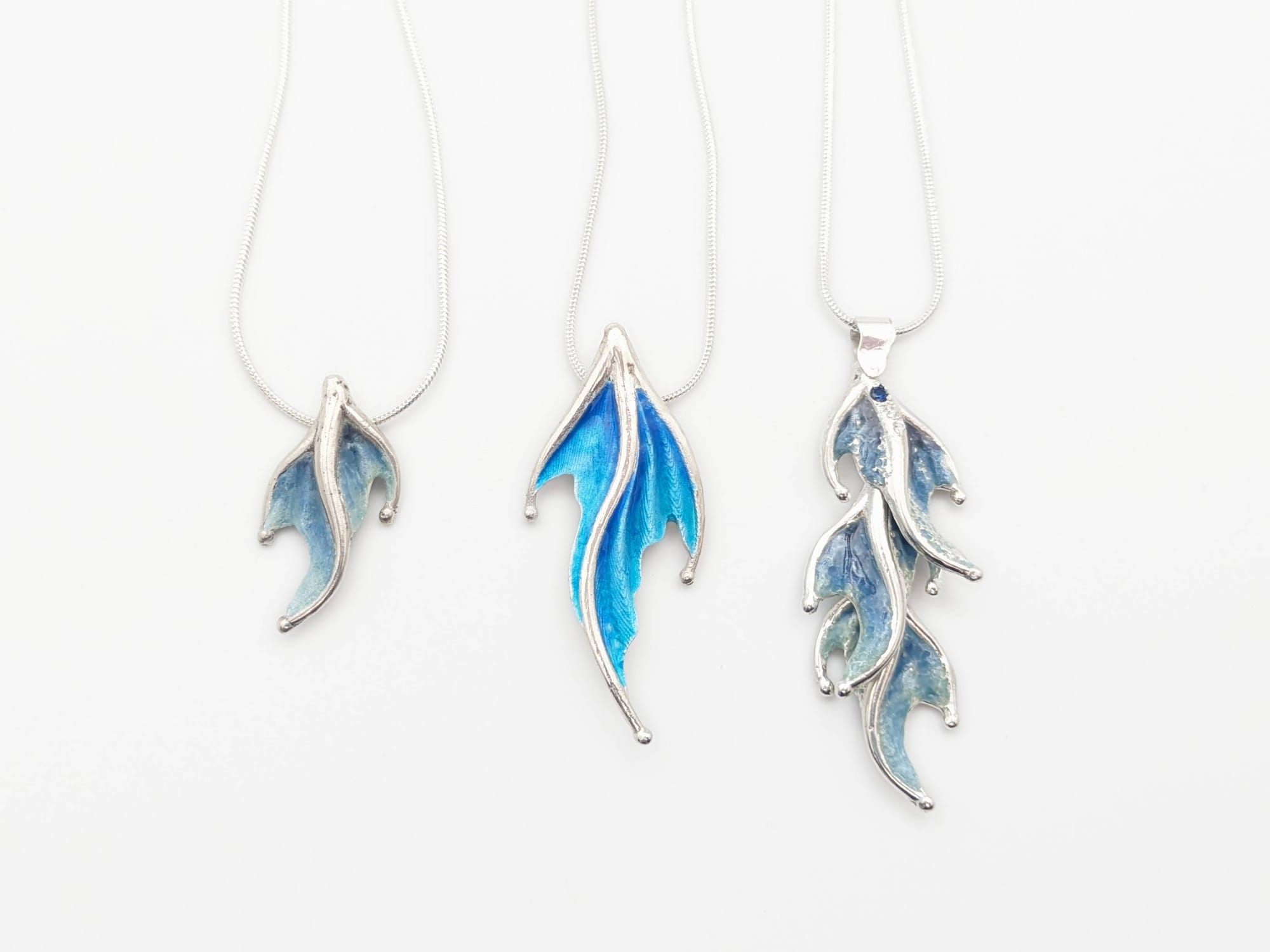
Then Mini and Micro happened (oops, the weird joys of 3D printing)
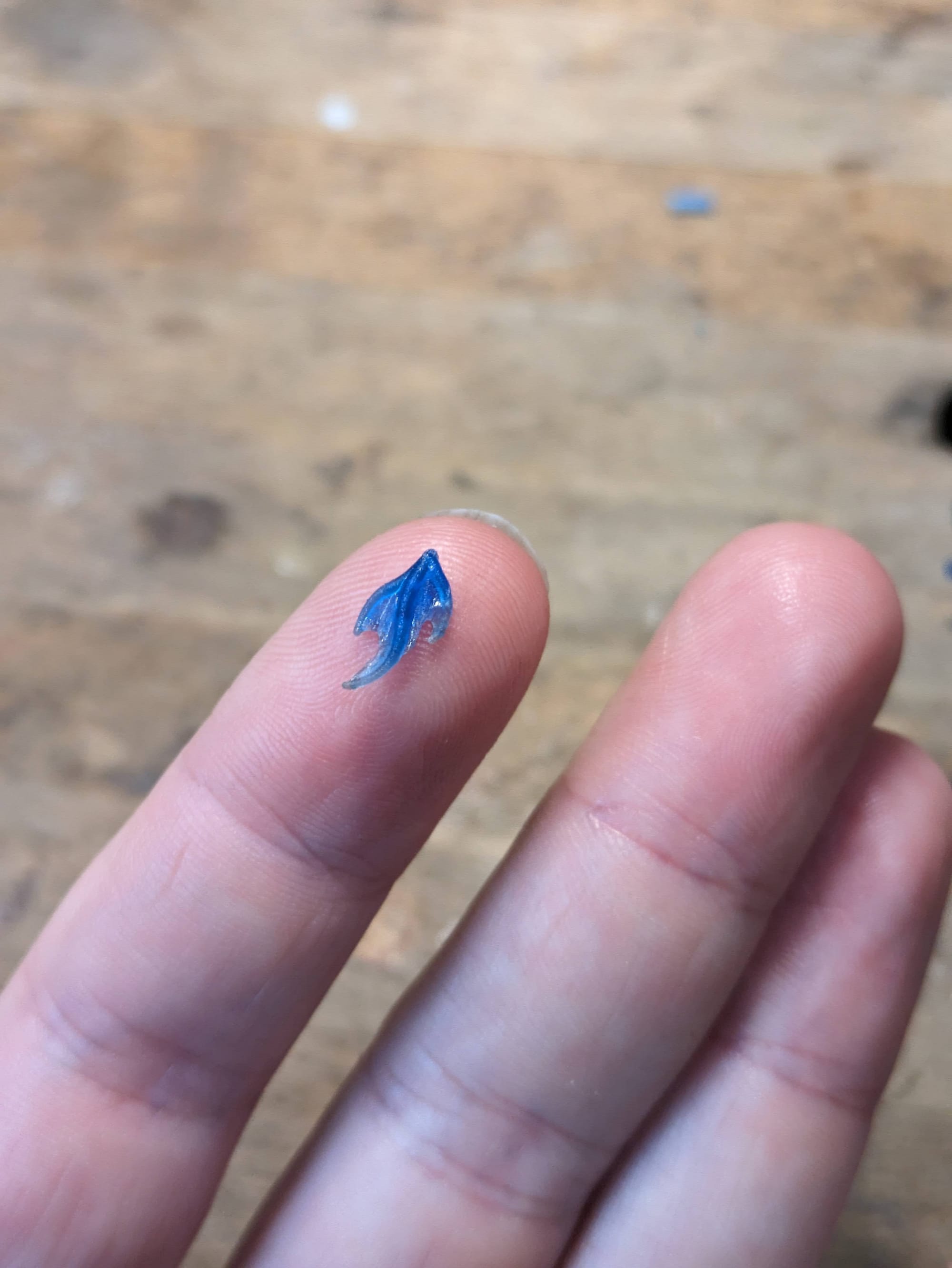
And now its growing again.
I want to create a bigger canvas for color without increasing the weight too drastically. I want to recreate the bold multi-piece artworks of college but at manageable material cost.
I want to try covering them in gemstones, and cutting holes to fill with plique-a-jour enamel. I want to get sculptural, but also dainty. I want to make the clasp integral and the length adjustable. I want to make a SeaDragon tennis bracelet. I have an idea for a ring?
I want to see where this goes.
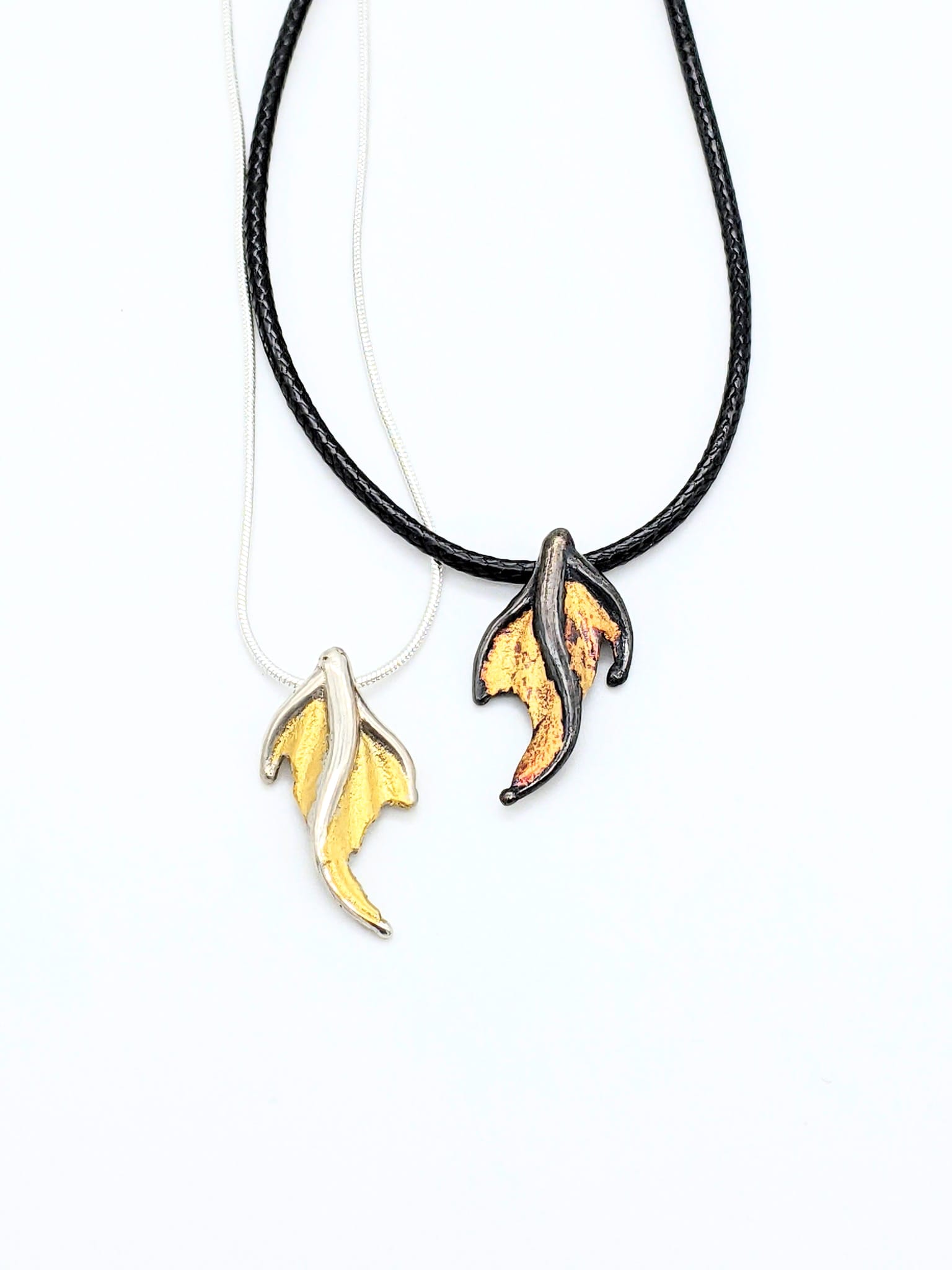